In the current manufacturing reporting landscape, data-driven decision-making is no longer a luxury—it’s a necessity. One of the most powerful tools in this ecosystem is Power BI, Microsoft’s business intelligence platform, which seamlessly integrates with Business Central to deliver actionable insights through advanced manufacturing reporting.
The Manufacturing Challenge: Turning Data into Decisions
Well, data is abundant—production metrics, inventory levels, work center utilisation, and more pour in daily. However, raw data alone doesn’t equate to value. The challenge lies in transforming this wealth of information into meaningful insights that empower decision-makers to optimise processes and respond to market demands. Traditional methods like spreadsheets or disjointed reporting tools often fall short, leading to delays, inaccuracies, and missed opportunities.
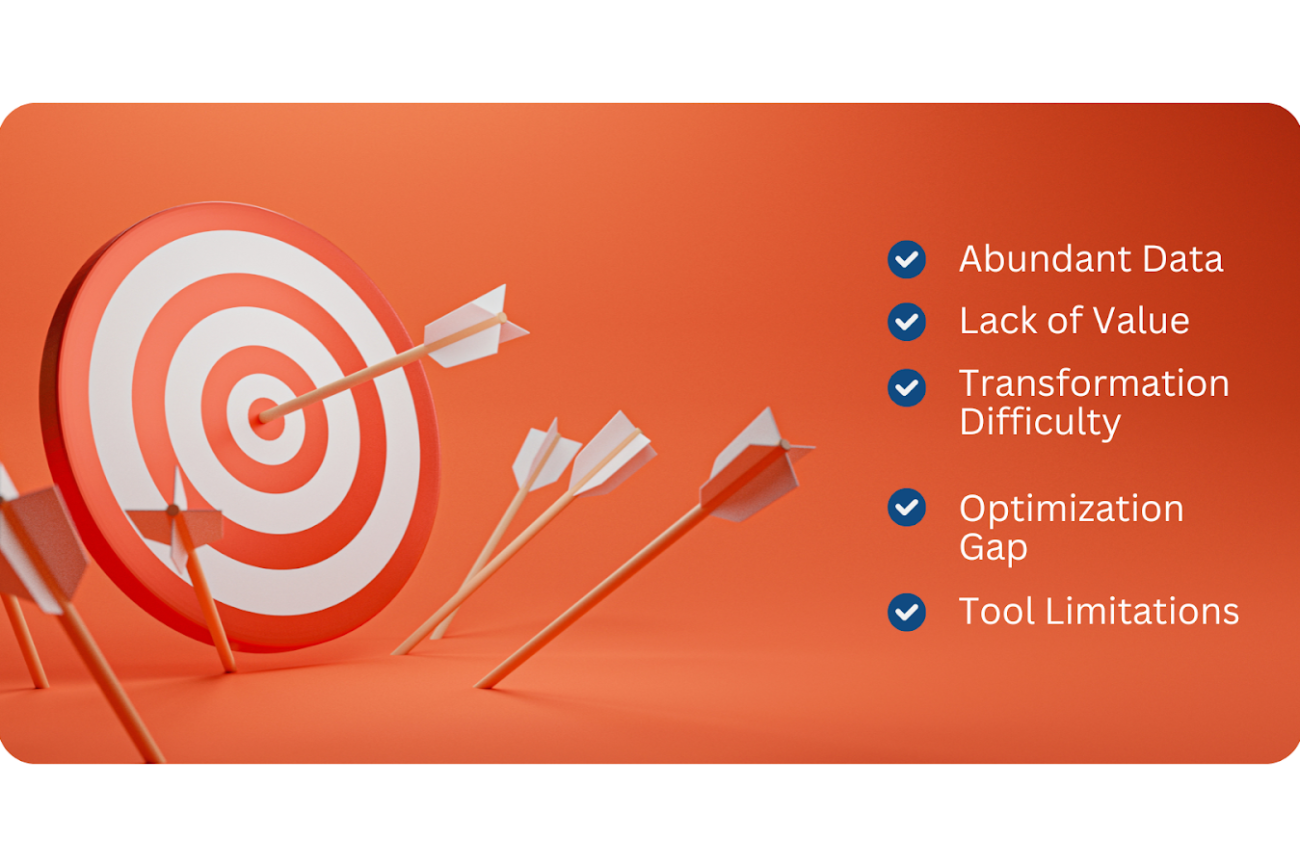
This is where Business Central and Power BI come in. Business Central serves as the central hub for managing manufacturing reporting and operations—handling everything from bills of materials (BOMs) and production orders to inventory and resource planning. Power BI, on the other hand, takes this data and turns it into visually rich, interactive reports that provide real-time visibility into every aspect of the manufacturing process.
Why Combine Business Central and Power BI?
Here’s why this synergy is a game-changer:
- Seamless Integration: Power BI connects directly to Business Central, pulling data in real-time without the need for complex integrations or manual exports. This ensures your reports are always up-to-date and accurate.
- Customisable Dashboards: Power BI’s intuitive interface allows manufacturers to create tailored dashboards that reflect their unique KPIs, whether it’s production efficiency, cost variances, or inventory turnover.
- Drill-Down Capabilities: Go beyond surface-level metrics. With Power BI, you can drill into the details—analyse specific work centers, production runs, or even individual components—to pinpoint issues and opportunities.
- Scalability: Whether you’re a small manufacturer or a global enterprise, Power BI scales with your needs, offering flexibility as your business grows.
- Accessibility: Cloud-based reporting means your team can access insights from anywhere, fostering collaboration across shop floors, offices, and remote locations.
Key Manufacturing Reporting to Master with Power BI
Here’s a list of a few examples that highlight how you can turn operational data into strategic advantages.
1. Work Center Utilisation
Understanding how your resources are performing is critical to maximising efficiency. Power BI can pull data from Business Central’s work center records to create a dashboard showing:
- Utilisation rates across machines and labor.
- Downtime trends and causes.
- Bottlenecks that slow production.
For instance, if one work center consistently exceeds capacity, you can use these insights to adjust schedules or invest in additional resources, ensuring smoother operations.
2. Production Order Variances
Cost control is a top priority for manufacturers. Power BI enables you to compare expected versus actual costs across production orders by analysing:
- Material consumption variances.
- Labor hours versus estimates.
- Overhead costs against budget.
Visualising these variances in a Power BI report helps you identify inefficiencies, such as overused materials or unexpected delays, and take corrective action before costs spiral.
3. Inventory Trends
Effective inventory management prevents shortages and overstocking, both of which can hurt profitability. With Power BI, you can track:
- Raw material usage over time.
- Stock levels versus demand forecasts.
- Slow-moving or obsolete inventory.
A real-time inventory dashboard ensures you’re always prepared to meet production needs without tying up capital in excess stock.
4. On-Time Delivery Performance
Customer satisfaction hinges on delivering orders on time. Power BI can aggregate production and shipping data from Business Central to report:
- Percentage of orders completed on schedule.
- Delays by product, work center, or shift.
- Trends in delivery performance over time.
These insights allow you to fine-tune processes and maintain strong relationships with your customers.
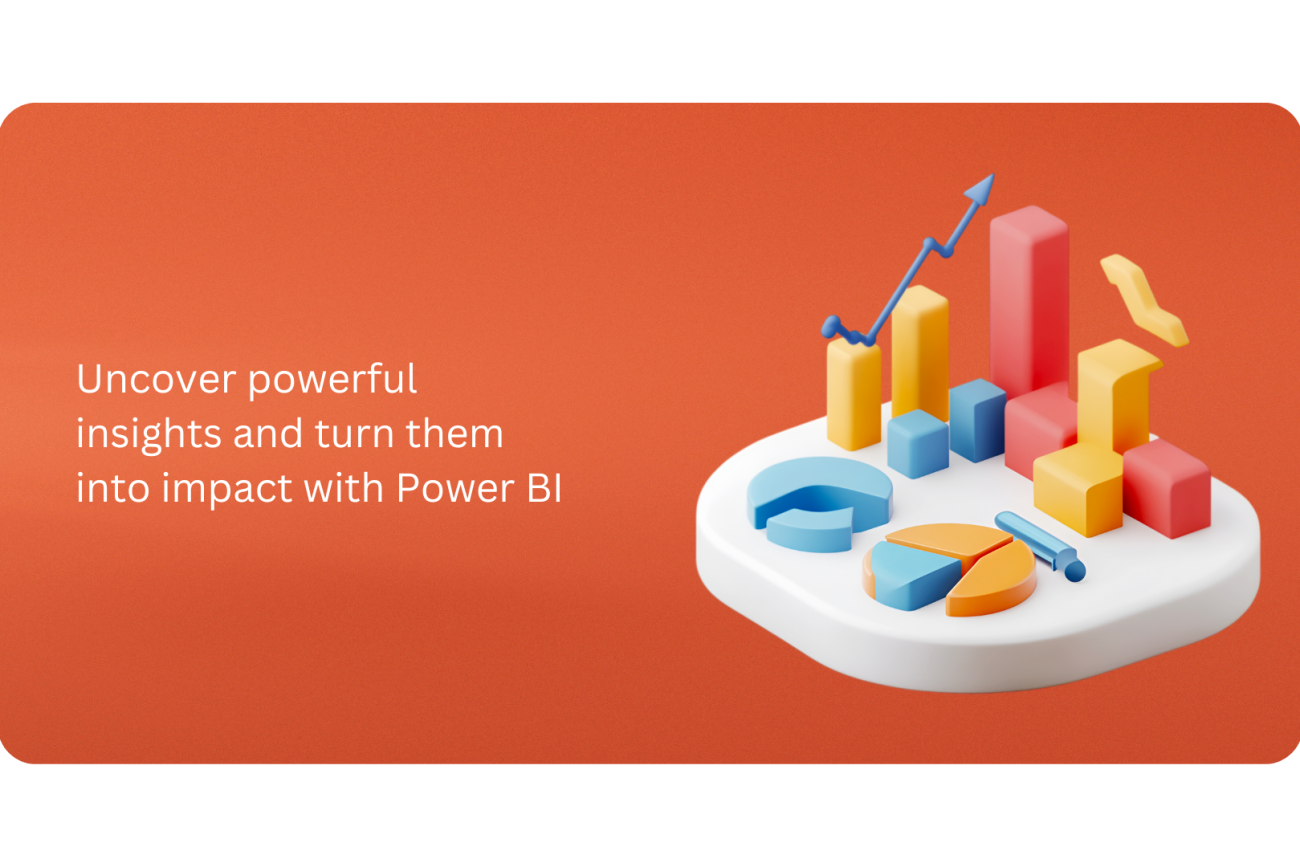
Getting Started: Best Practices for Success
Here are the best practices to master manufacturing reporting:
- Define Your KPIs: Start by identifying the metrics that matter most to your business—whether it’s throughput, cost per unit, or lead time. This ensures your Power BI reports align with your strategic goals.
- Leverage Prebuilt Solutions: Tools like Power BI Gold Manufacturing for Business Central (available on Microsoft AppSource) offer ready-made report templates, giving you a head start on implementation.
- Train Your Team: Empower your staff to use Power BI’s self-service features. With minimal training, they can customise reports and explore data independently.
- Iterate and Improve: Reporting isn’t a one-time effort. Regularly review your dashboards, gather feedback from users, and refine them to reflect evolving business needs.
- Partner with Experts: Working with a Microsoft Gold Partner ensures a smooth setup, from connecting Power BI to Business Central to designing reports that deliver maximum value.
The Future of Manufacturing Reporting
The latest enhancements in Business Central—such as those introduced in the 2024 Release Wave 2—have further strengthened its integration with Power BI.
Features like direct report access within the Business Central Role Center and simplified connector setups make it easier than ever to embed powerful analytics into your daily operations.
Looking ahead, advancements in AI and machine learning within Power BI promise even deeper insights, such as predictive maintenance and demand forecasting, positioning manufacturers to stay ahead in a competitive market.
Conclusion
Mastering manufacturing reporting with Business Central and Power BI isn’t just about generating reports—it’s about unlocking the full potential of your data to drive smarter decisions, optimise processes, and fuel growth.
Our experts at Osmosys have seen how this powerful combination empowers manufacturers to move from reactive firefighting to proactive strategy. Whether you’re looking to improve efficiency, reduce costs, or delight your customers, the tools are at your fingertips.
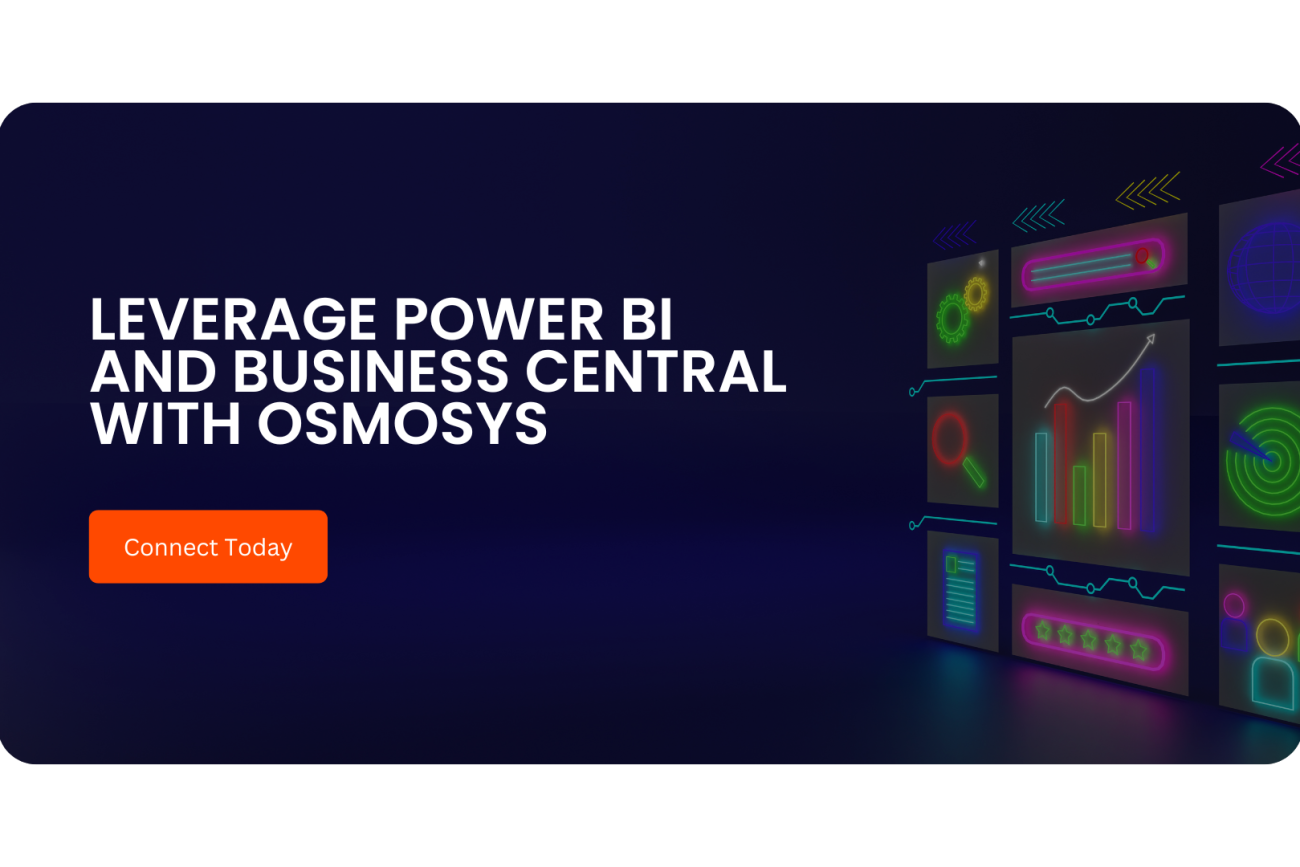
Ready to take the next step? Let’s connect and explore how we can tailor this solution to your unique manufacturing needs.